“The company adheres to the business philosophy of 'You Win, I Win' ”
Whether you want to create a textured cloth, weave a piece of furniture, or create a fabric with a strong surface, core spun yarn is the perfect option. This yarn is woven from twisted staple fibers. It is used in a wide range of applications, from leather and mattresses to quilts and rice bags.
The process of core spinning involves two steps: first, the filament is mechanically processed into a short, pre-drafted sliver, which can then be used for the subsequent spinning process. The sliver is fed over a tension device to ensure that it is positioned in a way that it will not slip out of the core. This process also ensures that the fibers are evenly distributed and the final fiber package is uniform.
The first step of core spinning is to set the condenser at a suitable temperature. This is important because the yarn has to be hot stretched to increase its strength and durability. Heat setting also helps in achieving a balance between the materials. The first nozzle pressure is also increased, which improves the sheath slippage resistance.
In the mechanical processing, the fibers are twisted and folded multiple times to strengthen them. The fibers are then wound into appropriate packages. This process also ensures that the yarn is free of impurities. The moisture content and color fastness are also important indicators of the yarn's quality.
After the mechanical processing, the colored filament is fed into the ring frame. The filaments are fed into the ring frame in such a way that they are twisted before they enter the front roller. The front roller is then nipped. This process creates the conditions for the carding process. The carding process breaks down the bundles into single fibers and removes any impurities. This process can also decompose the fiber bundles that have a strong adhesion.
A number of different spinning techniques are used to produce core spun yarn. These techniques are used to vary the amount of yarn, as well as the size of the thread. In order to ensure that the finished yarn has the required amount of twist, a compensatory tensioner is used.
Depending on the type of thread, it is also possible to add another type of thread to the core spun yarn. This can either be a continuous man-made filament yarn, or it can be a sticky fiber made from natural fibers.
The fiber should be held at a 90-degree angle to the core. This allows the fiber to travel up the core thread and wrap around it before going into the orifice. However, it is best to avoid twisting the thread too much. If it is allowed to loosen, the active twist can cause the yarn to ravel.
The ring spinning method is also used to produce core spun yarn. This method is economical and straightforward. However, it requires the core to be positioned in the center of the ring. If the center is not positioned correctly, the core can twist during spinning, causing a strip back.
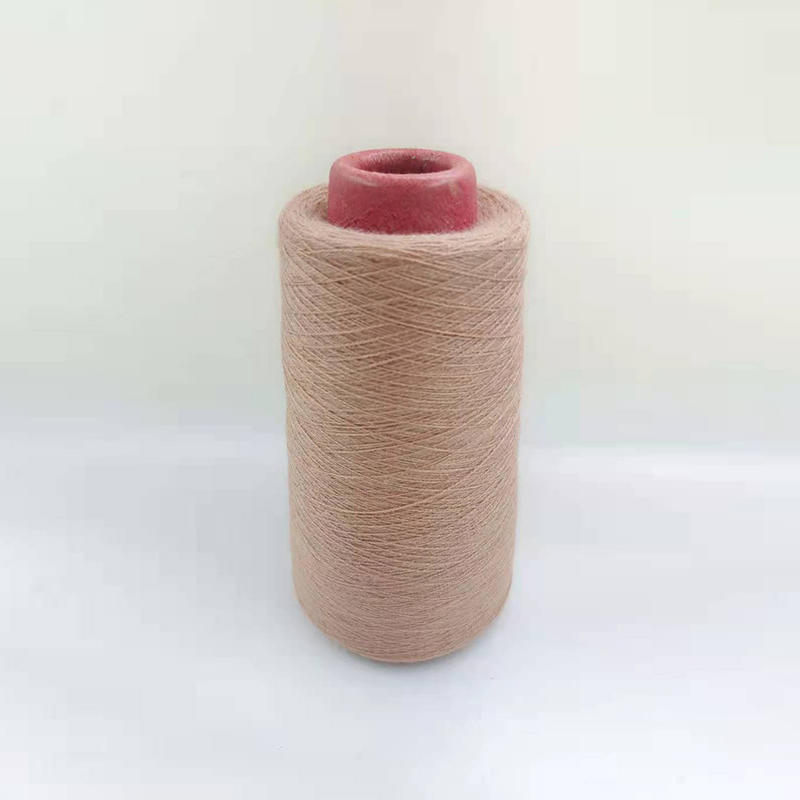
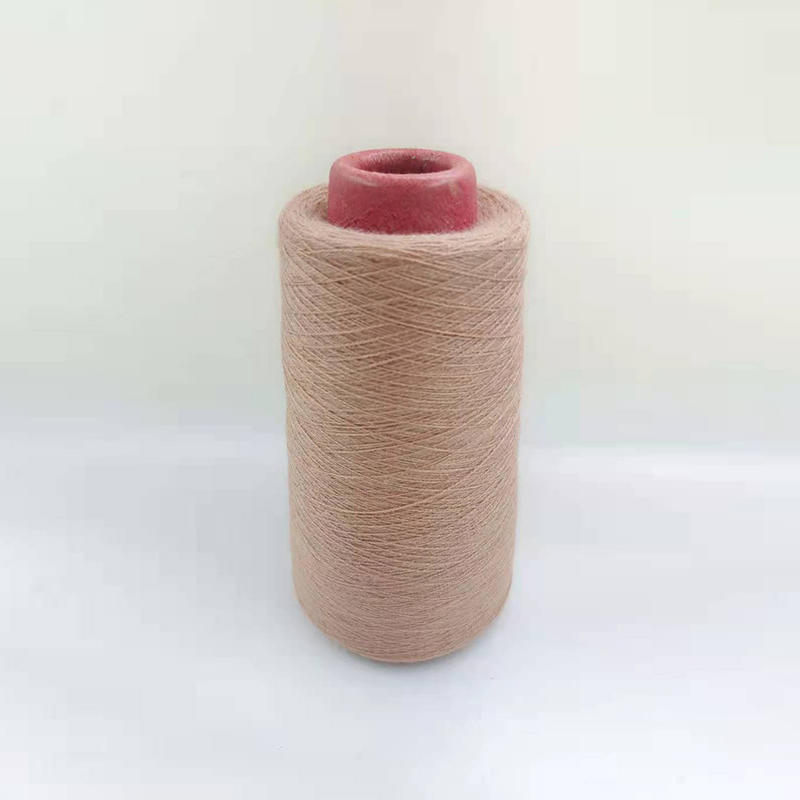
Product Name: Acrylic core spun yarn
28/2 Core spun yarn 50% Acrylic 28% PBT 22% Nylon Blend yarn
Origin: Jiangsu China
Brand: RHZ CORE SPUN YARN
Craft: RING SPUN
Material: 50% Acrylic 28% PBT 22% Nylon
Style: For knitting ,circular knitting ,flatting knitting
Colour: Various of colors according buyers requirements
Application: Outwear,sweaters,gloves,hats,socks etc
Feature And Advantage: Soft touch,imitation rabbit hair ,cashmere like